Today is the day of departure. We’re heading back home after over a week up north. I’ve decided to leave Blue-J up here to fully cure, since we’re not likely to be back until February. I decided to take advantage of the extra time by spraying more coats onto the body, and also stain the headstock after all.
I was nearly out of the Watco lacquer. The Duplicolor shipment had arrived on Friday, so I decided to give that a try on top of the Watco. After all, I had 4 coats of the Watco on already.
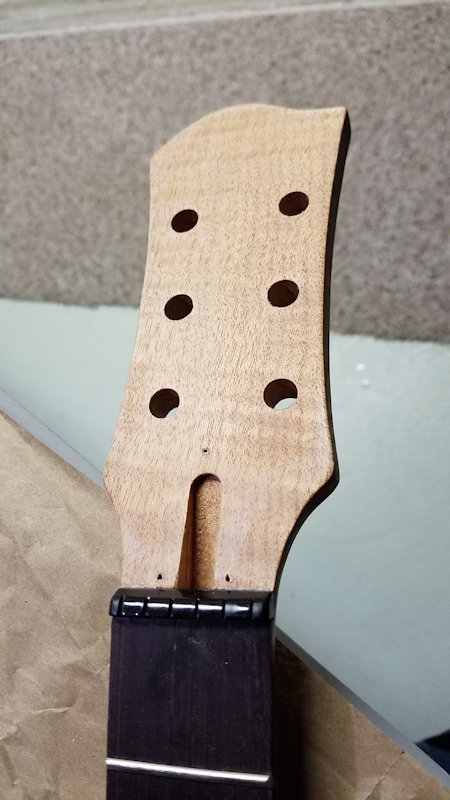
I removed the hardware and sanded down the face. I masked off the sides, nut, and most of the fretboard, and shoved paper towel into the truss rod cavity. I also backed the tuning peg holes with masking tape.
Stained with a higher concentration of the diluted blue tint, and sprayed clear in multiple coats along with the body and got this.
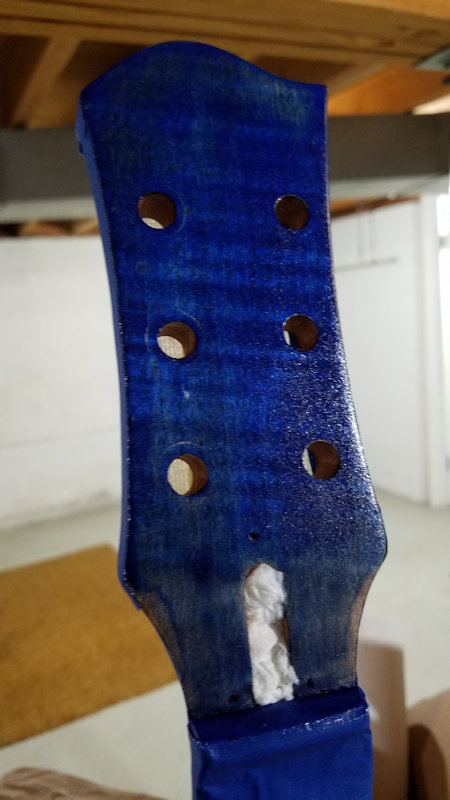
I can see where it was more difficult to sand down by the nut and at the top of the headstock because I didn’t get all of the shipping sealer off. But, another lesson learned.
I reassembled the basement, putting the window panes back into place and cleaned up my work area. I moved the guitar more toward the center of the basement and moved the table underneath it; I had this sudden fear of the suspension wire giving out and the body crashing to the floor, splitting in half.
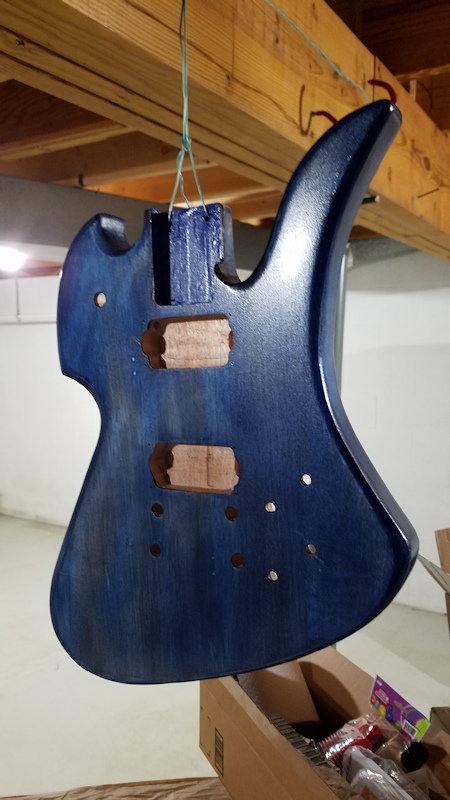
The Duplicolor sprayed a lot more finely so there’s more pebbling/orange-peel than the Watco. Duplicolor also smells a hell of a lot worse (not to say that the Watco was like smelling a pot of pasta sauce on the stove or that breathing the fumes is a good idea, but still…).
On the first coat, I was too heavy handed because I wasn’t expecting the velocity of spray compared to the volume. I ended up with two drip spots on the body that I didn’t notice until the first coat had dried for almost 2 hours. I gently sanded down with 400-grit, cleaned the areas, and sprayed the 2nd coat (again, 3 passes per coat, with intervening dry time).
I let the work dry overnight and inspected during workstation clean-up. The spot under the horn is barely noticeable, but the one on the back is still there though not nearly as bad as when I first noticed it.

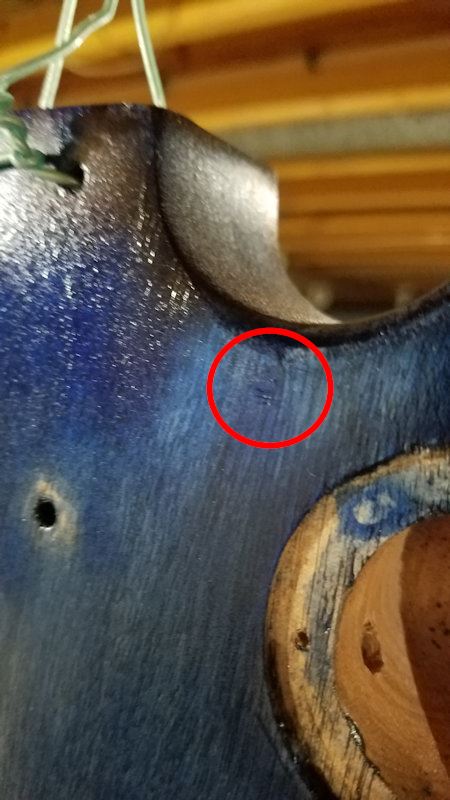
I hope to get a better idea of repairing this in February.
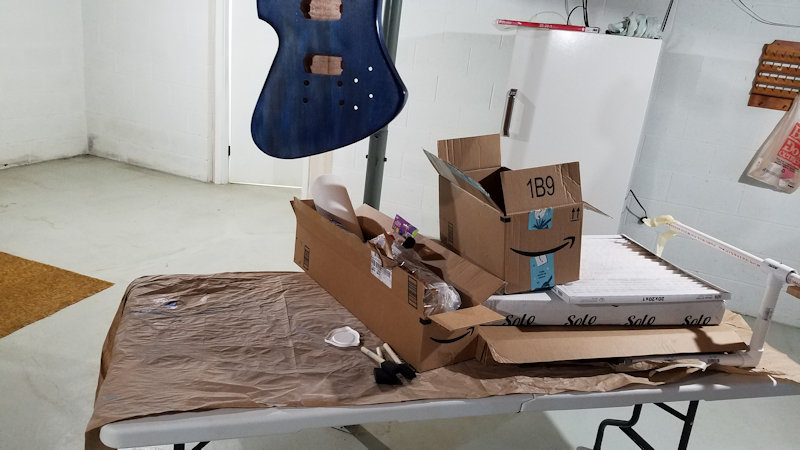